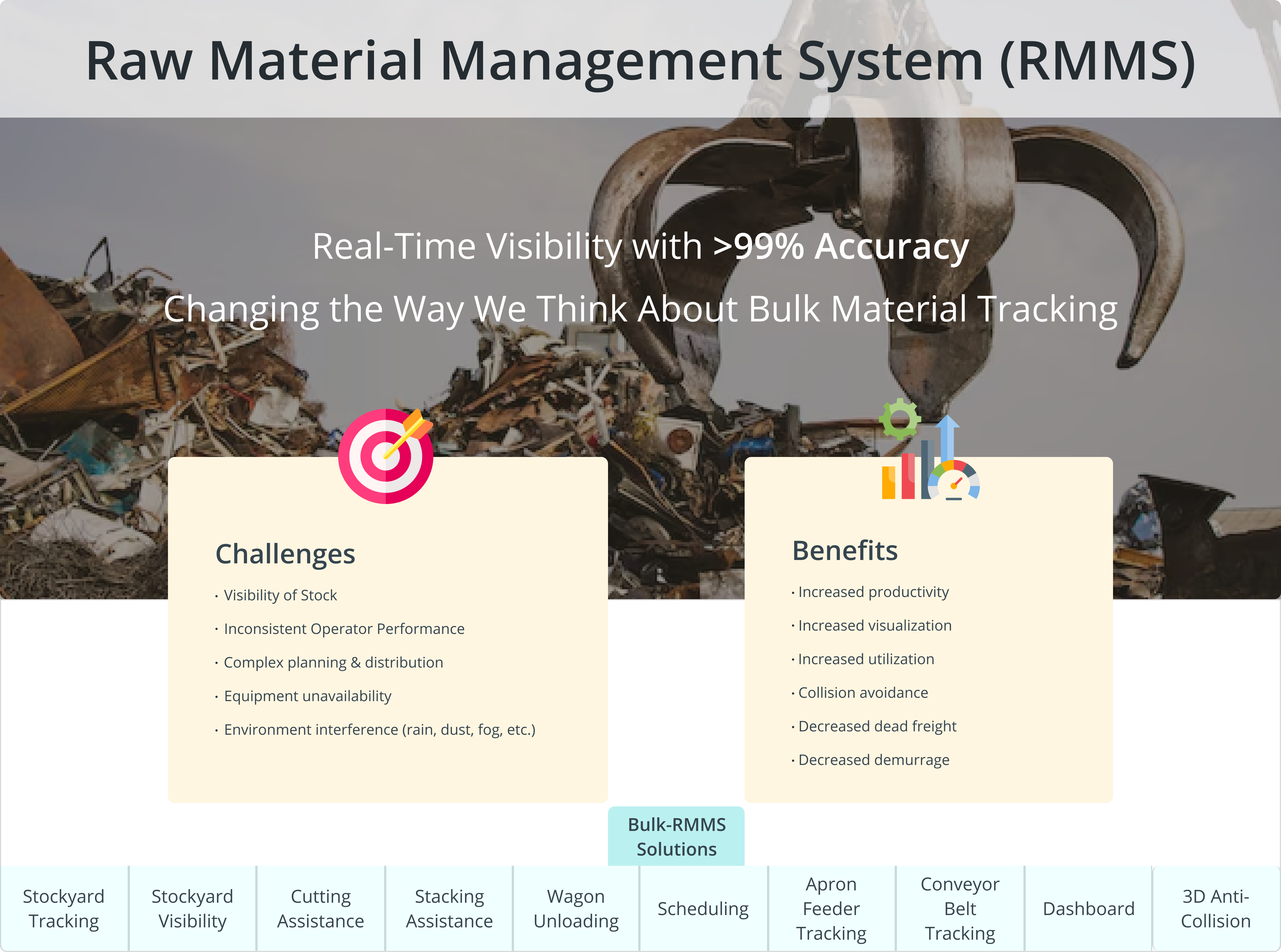
Stockpile Tracking System
Stockpile Tracking System
Stockyard solution is designed to bring visibility across the organization and manage the stockyards optimally. It brings a systematic approach to plan and operate the stockyard activities and utilize man & machine efficiently. Hind Industec uses 2D Radar scanning system to produce the real time information of the stockyard. The solution helps to eliminate problems like 'air reclaiming', 'ground digging' and 'collision risk' by continuously monitoring the stacking or reclaiming operation and their position on the real time basis.
The variety of operating methods and the multiplicity of materials has traditionally made it difficult to rely on anything else but skilled operators and to some extent semi-automatic or remote systems. However with the Hind Industec, it is now possible to implement a completely unmanned operation for any combination of Stacker/Reclaimer. Hind Industec offers a fully automated system which requires one operator presence in the central control room (CCR) to control a complete stockyard.
- Visibility
- Tracking
- Scheduling
- Stacking Assistance
- Cutting Assistance
- Anti-Collision
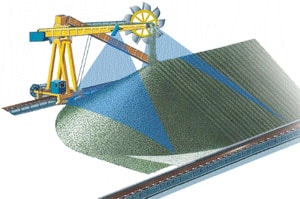
An effective and smart business decision can turn the situation of the company but it is merely a dream in absence of an integrated system with complete visibility on real time basis. The supply chain visibility of stock position at all the operational units, planning, logistics and operation can optimize the process and increase the productivity. The revolutionary technology brings the bulk inventory information online and on real time basis.
The stockyard solution offers a 3D graphical view of the actual stockpile boundaries and the current location of the equipment inside the yard on a real time basis. Changes in the stockpile surface caused by external interferences, such as dozers or pile collapses are also tracked and a quick overview of the inventory type and quantities stored around the stockyard together with a more detailed analysis tool to zoom and view cross- sections and effective utilization information.
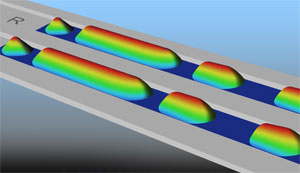
Data is valuable only when it is accurate and accessible on time. All the technological advancements for geological and mechanical modeling are for expertise and interest of the department but data collection is still being done in desperate system. The inventory tracking module keeps track of all material handled by the stockyard equipments. The properties like inventory volume, type, grade, density, stockpile boundary etc can be accessed through web based system on a real time basis. There are different colors to depict different stockpile with respect to their properties like grade, age, density etc. and it is for easy visual identification in the graphical overview. A reporting tool means you can extract vital information about any material stored in the stockyard database, e.g. material quantity, location or grade which is important when it comes to blending different grades of material to obtain a specified combined product, age etc.
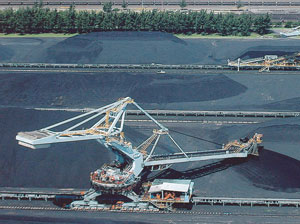
As the demand arises, the system generates a schedule for required equipment and the same schedule is converted into work order for individual equipment. Each scheduled task comes with an estimated time to perform the work order and accordingly queued to perform the Task. It helps to track the equipment performance and guide the operator to execute the task without any manual intervention.
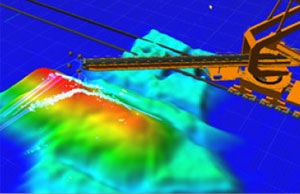
This feature allows to calculate the space requirement to stack incoming inventory. According to the ship/rake arrival plan, the system receives dispatched weight manually and then it will calculate the space requirement and suggest the yard area where inventory can be stacked. It also assists to control the boom height while stacking to control dust.
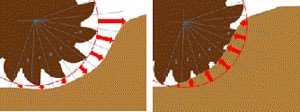
The Cutting Span Depth Estimation feature allows to monitor the depth of bucket cuts into the stockpile. To enable this control, the radar array measurement section is virtually split up into n equal-sized zones (illustrated by blue lines in image below) that are arranged within an angle of about 100° degrees. The zones are numbered from 1 to n and from the lowest point of the angle to its peak. The depth of the cutting circle into the stockpile is continuously updated and returned for all zones.
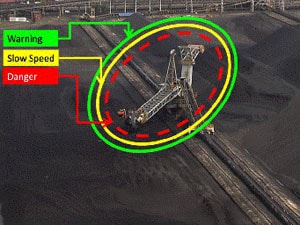
The anti-collision and collision avoidance assistance uses the radar positions and automatically alerts an operator if machines are within the vicinity of the outer allowed operations. The system will generate alert and beep in case it runs in manual mode and stops equipment in case it is on auto mode. The system provides 3D visualization of anti-collision zones in 3D.
Wagon Loading and Unloading System
Wagon Loading and Unloading System
Wagon Loading System provides a high-precision train loading system, using wagon and material-specific optimized loading profiles as per the rated capacity declared by the government and available residual material inside each wagon. To measure the exact volume/weight of the wagon and online filling height of the wagon, Hind Industec uses 2D radar technology. The system also gets connected with the existing railway system to exchange information.
- Challenges
- Features
- Benefits
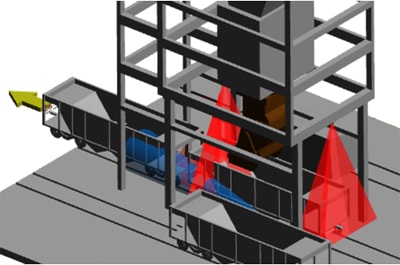
Identification of Residual Material :
Train loading stations can be the bottleneck for bulk material. Wagon capacity utilization, existing residual material inside a wagon, time to fill a wagon, identification & sequence of wagon and spillage while shifting wagon are few challenges which directly impact on the overall performance and profitability. The wagon loading becomes costly when the above parameters are not known on time. The radar based Hind Industec system takes care of all the parameters. The auto scanning of wagon, auto identification of edge frame of wagon, scanning of residual material if any, prediction of volume as per rated capacity minus residual material lying inside wagon are some of the key functions to optimize the loading facility.
Spillage
Spillage of material during loading of wagon is a major concern. It happens when the height of the material is not inline with the rated capacity and when the chute gets shifted to new wagon. In absence of the real time filling height measurement system, the operator works on eye estimation which results into either under loading or overloading of the material. In case of under loading, less material is getting loaded & transported whereas overloading of material means spillage while moving the train as well as demurrage. The chute gate should be shifted only when the mouth of the chute is on top of wagon where material has to be filled. In absence of real time position and edge frame of wagon measurement system, the slide gate of the chute gets shifted earlier than expected which results into spillage. The loading station reports 3 to 4% of spillage of material every rake/wagon.
- High-precision 2D Radar scanners to efficiently scan empty & loaded wagon
- Identify incoming wagons by type (differing dimensions) and their sequence no.
- Detect the edge frame of incoming wagons (irrespective of type).
- Measure the volume of residual materials from previous loads in the incoming wagons.
- Measure the volume of material passing through the belt at the rake loading station.
- Detect the height and volume of the filled material to allow for filling to maximum load height and shift the filling chute to next wagon.
- Measure the moving speed of the rake loading machine in real-time.
- Optimal utilisation of wagon capacity reduced transport cost
- Shorter lead time - increased manpower utilisation
- Full wagon utilisation without risk of overloading - control demurrage cost
- Reduced/eliminate demurrage - increased profit margin
- Reduced spillage - reduced wastage
- Reduced operator staff - Manpower saving
Belt Tracking System
Belt Tracking System
Conveyor belt tracking system is designed to provide belt Speed, Load of material on conveyor belt, and misalignment of belt. The 2D Radar sensor with inbuilt motion sensor is used to measure all three Parameters on a real time basis and send alters to the control room operator in case of deviation. The system also provides interlocking facility where the conveyor belt will be stopped in-case any KPI touches to their upper limit.
- Features
- Benefits
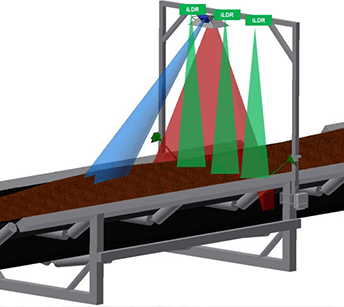
It's a modified version of conveyor belt solution for the measurement of material flow and material behavior on conveyor belts. The solution is based on an array of high speed measuring Liner Dynamic Radar sensors (1000Hz measurement frequency with a precision better than 1mm), a speed sensor Doppler Velocity Radar and an Dual Range Radar. Apart from detecting oversize rocks, this solution will also provide the volume flow of the conveyor belt with high precision
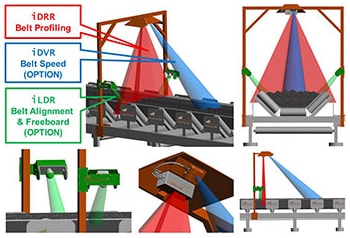
The belt tracking system is designed to provide belt Speed, Load of material on conveyor belt, and misalignment of belt. The 2D Radar sensor with inbuilt motion sensor is used to measure all three Parameters on a real time basis and send alters to the control room operator in case of deviation. The system also provides interlocking facility where the conveyor belt will be stopped in-case any KPI touches to their upper limit.
Ship Unloader System
Ship Unloader System
A single data source to provide real-time visibility of equipment, inventories, and associated quality levels across the supply chain. It helps organization to increase the efficiency of the equipment, manpower and minimize / eliminate the risk like collision, overloading / under-loading of inventory etc. Hind Industec provides an integrated view that includes process and quality information and it helps in real-time decision making, dynamic responses to process variations, and efficiently satisfying order specifications.
- Challenges
- Features
- Benefits
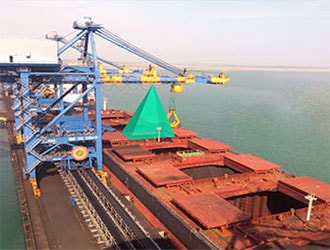
Equipment Efficiency :
The equipment efficiency depends on their utilization and it can only be evaluated when the efficiency of equipment is measured on a real time basis during operation. The RMMS tracks the operational efficiency of each equipment on the real time basis and compare with their SOP. It helps to increase the productivity of the equipment by more than 10%. It also helps to provide the real time information of inventory being handled by the equipment.
Inventory Loading
The conventional way to know the material weight inside the hatch of a ship is thou draft weight of ship. This is internationally accepted system and no one challenges this system but everyone is looking for some alternative system to validate the weight. The Hind Industec system tells the exact volume of the material gone inside the hatch.
Hatch Scanning
Looking inside hatch from a far distance is a real challenge. The 2D Radar helps to scan the material falls inside the hatch and the surface of the pile. This system guides operator to fill material at the maximum allowable height and weight. It also helps to dress the surface of the pile.
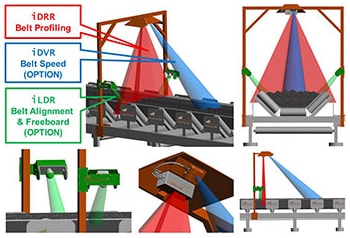
- High precision 2D Radar scanners to efficient scan the material inside a hatch.
- Detect the height and volume of the filled material to allow for filling the material inside hatch to the maximum allowed limit.
- Measure the volume of material passing through the conveyor belt to the ship loading station.
- Measure the equipment efficiency.
- Detect the gap between ship navigation system and GSU to avoid collision.
- Detect the edge frame of the hatch to avoid collision between grabber and hatch edge.
- Detech the object (Dozer) moving inside the hatch to avoid collision between grabber and dozer.
- Increased operational visibility - faster and smarter decision.
- Increased safety - increased equipment life and improved operational environment.
- Optimal utilization of equipment - increased equipment productivity.
- Shorter lead time - increased manpower / equipment utilization.
- Reduced / eliminate demur-rage - increased profit margin.
- Optimal utilization of ship hatch capacity - reduced transportation cost.
Enquiry
Need Help? Send Enquiry to Us
Address
Unit-104, Tower C, Rail Vihar,Sector 15, Part 2, Gurugram-122001, Haryana, India
Call Us
+91 94296924650
Email Us
info@hindindustec.com