Ladle Tracking System

"Ladle Tracking System does not merely tell where ladles are; it also tells how fast ladles are moving around in the shop and what their current lives are."
A real-time Ladle Tracking System (LTS) provides complete information about ladle be-it the ladle heat information, exact ladle position, ladle idle time, ladle life, exact contact time with hot steel, causes of delay and maintenance requirement. The system detects exact arrival & departure time for each ladle to the processing area along with it's idle time. From the information supplied by the automation system, the LTS maps the heat information, exact processing time and temperature profile for each ladle.
The LTS captures all the information from the maintenance work performed on a particular ladle and gives a clear understanding of the ladle availability for future heats. The system also maintains past history of the ladle which helps supervisor to analyze ladle profile. Ladle profile includes ladle life, heat-wise history, temperature profile, aging etc.
- Equipments
- Scheme
- Features
- Benefits
- RFID Tag
- RFID Protection Armor
- Stations
- Antenna
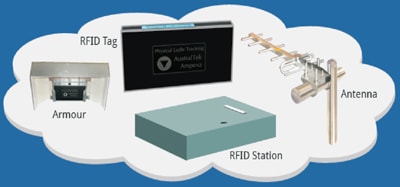
The RFID tags are passive and use a modified form of the RFID reader's own signal to transmit data. Essentially, the tag reflects the RF signal transmitted by the reader and embeds its unique ID by modulating that reflected signal. The unique identification number will not change during the lifetime of the tag. The tags can be read from several feet away and they don't need to be on the line of sight of the reader. The system detection distance between sensors and antennas is recommended to be limited to 22 meters; however the detection distance has been site-tested up to 30 meters.
In order to protect the RFID Tag from both high temperature and collisions with other equipment, the RFID tags are installed inside a special protective cover called "armor", which is welded to the ladle wall. The armor location on the ladle depends on ladle wall temperatures and where it will be safe from collisions and from signal interference. The armor keeps the sensors' temperature range within working levels to allow correct data transmission. The armor protects the sensors from collision damage, from hot metal splashes, and from slag falling from top of the ladle. The armor is manufactured in special steel with several layers of insulation on the internal side where the RFID tag is located.
The RFID readers are installed inside the stations, which are NEMA 12 enclosures that protect the RFID readers from the environment. The stations have forced ventilation to keep the RFID reader within working temperature ranges and all necessary electrical distribution for powering and protecting the equipment. The RFID readers can manage up to 4 different antennas, which are individually connected to the reader with coaxial cable. The high gain, directional antennas are directed to the locations where the ladles need to be detected.
The antenna's gain, measured in dBi (decibels relative to isotropic radiator), is selected depending on cable length and the maximum distance between the antenna and the ladle location. Typically 3, 6, 9 and even 12dBi antennas can be used. During system installation, each antenna is carefully installed, oriented and calibrated to cover a defined area of the plant, which we call spots. Typical spots in a melt shop are the tapping area, cranes, LF, ladle cars, caster turret arms, and pre-heaters.
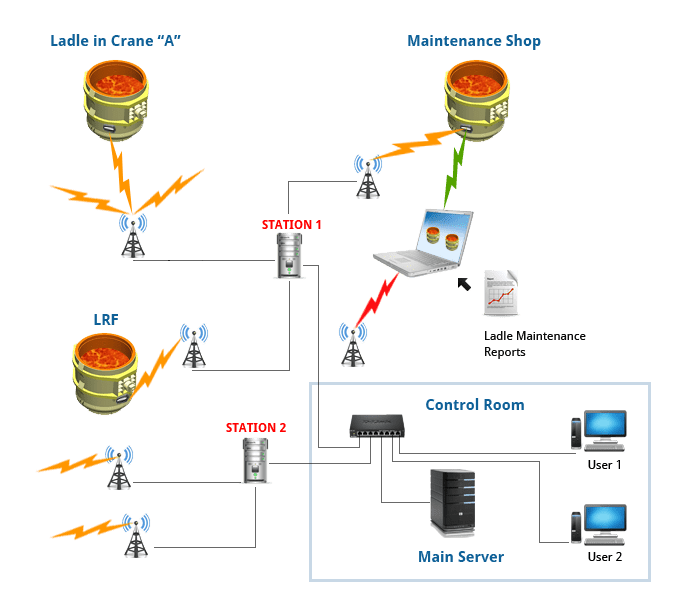
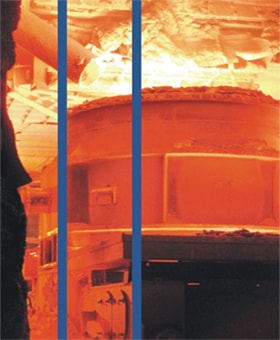
- Travel time and other Ladle/Torpedo movement statistics
- Plant Mimic with Graphical Ladle/Torpedo Movements
- Keep track of relationship between Ladle - Heat - Processes (production information required)
- Keep the status of all supervised objects and their alarms
- Log recording of alternate operations such as ladle maintenance etc.
- Provide information for Reports such as "Idle Times", "Empty Times", "Average Travel Times" etc.
- Totally expandable (Detection stations as per need)
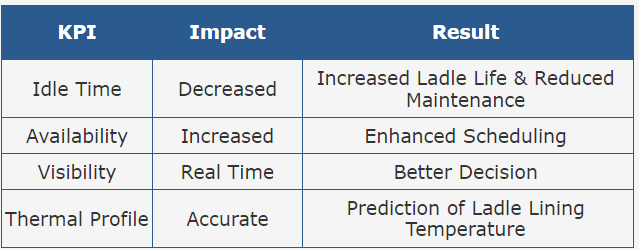
Ladle Monitoring System
Ladle Monitoring System

The Ladle Monitoring System provides an accurate and reliable measurement solution to ensure plant safety and help set maintenance schedules in the steel plants across the world.
- Ladle Life
- Benefits
- Ladle Recognition
- Ladle Identification
- Ladle Analysis
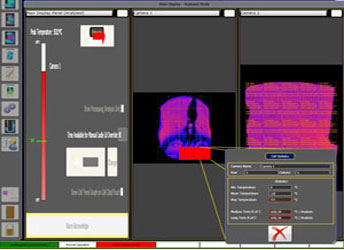
The software features integrated intelligent shape recognition technology which is configured to identify all the ladle profiles used in plant whilst excluding other elements. This system ensures false alarms are not reported as a result of hot background objects. Data capture and analysis starts once the software has confirmed the presence of a ladle in the camera's field of view.
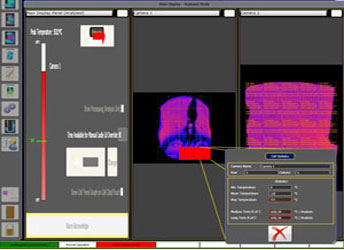
Vessel Manager stores the temperature data for each individual ladle on plant for long term analysis and trending. The ladle id comes from ladle tracking system and based on ladle id, the temperature data from each thermal imaging camera is analysed.
Ladle Monitoring System features a fully configurable analysis system, allowing a grid to be overlaid on the thermal images. Each cell in the grid provides the min/max/mean temperature for that area, along with rates of change, position and camera id. The live temperature data from each cell is compared with pre-configured alarm thresholds - any discrepancy between the live data and the predefined limits will raise an alarm. The software's on-screen analysis grid clearly highlights the location of the alarm, giving the operator immediate indication of a potential problem.
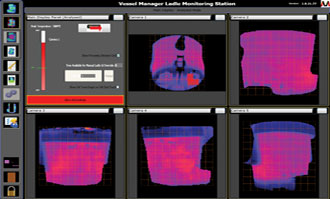
- Improved safety
- Prevention of break-outs
- Extended lifetime of ladle refectories
- Evaluation of different refectories
- Detection of problematic areas
- Cast refractory uniformity
Enquiry
Need Help? Send Enquiry to Us
Address
Unit-104, Tower C, Rail Vihar,Sector 15, Part 2, Gurugram-122001, Haryana, India
Call Us
+91 94296924650
Email Us
info@hindindustec.com